Crossing the Little Muskingum River
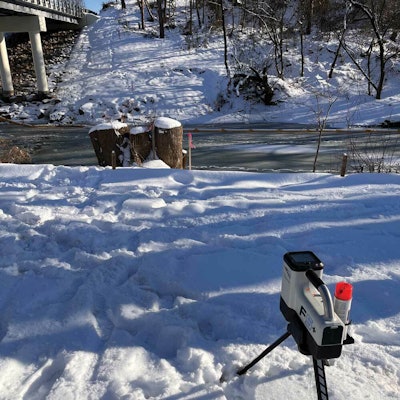
Each HDD installation can be considered unique in that site conditions, scope of work, depth, geology and other conditions contribute to the variability of a job. But many of them fall into categories where only a few of these conditions are out of the ordinary. And then there are other bores where several factors contribute to the complexity of an installation, one that requires different solutions than most days.
One such installation took place in Marietta, Ohio, in January. The bore involved the crossing of the Little Muskingum River and the installation of a 6-in. HDPE gas line.
Full Bore, a drilling contractor out of West Virginia, had been contracted to install the pipe under the river as part of a larger gas project. One of the requirements for the crossing was that annular fluid pressure be monitored during the pilot bore. Inadvertent returns are typically caused by the drilling fluid pressures being higher than the soil can support, and in those cases the fluid will often find a path to the surface. One of the ways to mitigate that risk is to monitor the annular fluid pressure and how they are trending.
The crossing was designed to be about 650 ft long and was expected to reach depths in excess of 60 ft, mostly due to an elevation increase on the far side of the river. The width of the river at the crossing was about 100 feet. The geology consisted of rock which brings its own complexities.
Full Bore owner Robbie Cobun chose his Ditch Witch AT100 All Terrain drill for this bore given the ground conditions and an AT Tricone bit to contend with the rock. The AT machine has a thrust force of 70,000 lbs and a pullback force of 100,000 lbs and with the inner rod providing rotation to the drill bit, a good solution for this project.
The bore itself, given the ground conditions, the depth and the fluid pressure monitoring requirements was going to present a challenge but on the day of the bore, mother nature had decided to bring the elements into play. The temperatures were below zero and the ground was covered in snow. The freezing temperatures led to issues with transporting water to the site and once on site, all the equipment on site had to be winterized.
Due to the planned depth and the necessity to monitor fluid pressure, Robbie decided to use the DigiTrak Falcon F5+ with the 19-in. Falcon transmitter. The Falcon transmitter has a built-in pressure monitor which reads the annular fluid pressure multiple times per second, averages it and sends pressure data to the receiver every three and a half seconds or so. This data, along with the standard clock, pitch and depth data is sent to the remote display at the machine where the driller will therefore have the pressure data available. Any changes in the pressure data are worth noting, increases in particular. An increase in the annular pressure can signify problems with drilling fluid returns and the solutions is often as simple as swabbing, which cleans the hole, returns fluid flow and thereby reduces pressure.
The pilot bore started early on the morning of Jan. 25 and progress was slow but steady. The bore plan called for a gentle curve through out the bore and Full Bore was able to maintain that curve and follow the profile. The bore was recorded using Log While Drilling (LWD) to create a bore profile, as well as keep track of all the other readings, including the pressure. The pressure readings on the near side of the river were in the range of 25 to 35 psi and the returns were normal. As the depth increased, the pressure naturally increased and on rod 15, 200 ft into the bore the drill had reached the river’s edge. At that point, the bore was a little over 38 ft deep and the average pressure for that 15th rod was 33 psi with the maximum reading having been 75 psi. Locating information was solid and both depth and pitch readings generally agreed with the plan and even as the depth increased, guiding the bore was never an issue.
Although inadvertent returns were a concern, special care needed to be taken while crossing the river so there were inspectors on hand for monitoring.
Crossing the river itself took about two and a half hours and the during that time, fluid pressures averaged between 33 and 37 psi. One of the indications of an inadvertent return is a sudden drop in annular pressure as the drilling fluid escapes the bore hole. No such pressure drop was recorded. As the bore continued an incline on the far side of the rive resulted in increased depth readings and fluid pressures and the maximum depth of 64 ft was reached about 420 ft into the bore on the 31st rod and that is where the pilot boring was halted for day.
As the terrain leveled off and coupled with the bore taking a positive pitch, the pressure readings decreased and the fluid pressure on the last few rods were around 20 psi.
The pilot bore ended up being 668 ft long. The cold weather added to the complexity of keeping the equipment running but the drilling machine and locating system performed very well.
This installation benefitted by the planning undertaken by Full Bore and others associated with the project. Having a bore plan is crucial when drilling rock since it is much less forgiving than softer soils and course corrections are much more difficult.
Selecting the proper drill rig, tooling and other associated support equipment plays a crucial role and, in this case, the depth and the real time fluid pressure monitoring requirements led to the choice of locating system.
The Little Muskingum River crossing is one of many examples where horizontal directional drilling has proven to be the optimal solution for the installation of utilities in areas of ecological concern.