The DCI Engineering Team: Bringing Innovation & Quality to the World of HDD
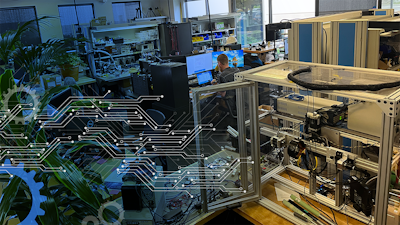
What does it take to bring a product to market? That’s a pretty loaded question and certainly unique to different businesses, but for DCI’s purposes, we count on a strong customer focus when defining new product plans and the highest level of engineering innovation to create winning products. Speed, experience, astute observations, collaboration – these are all things that can help make the difference between a happy customer and missing the window of opportunity altogether.
That’s why DCI, since the company’s inception 30+ years ago, has always prioritized doing things in-house whether it’s design, fabrication, or testing. It’s that hands-on, start-to-finish product development that makes DCI an engaging work environment for mechanical, electrical, and software engineers alike. Add on the fact that the majority of DCI’s manufacturing also takes place on-site in Kent and you have quite a unique situation where things move quickly.
“It’s hard to overstate the value of having manufacturing not only domestically, but in the same building as the engineering team. Engineering can provide faster responses for issues that arise, and since we have daily contact with our manufacturing partners, we naturally have better teamwork and alignment on goals. And since we are in the same time zone and in the same building, we are co-located for rapid meetings and quick solutions when needed,” says Larry Pendergrass, DCI’s head of engineering.
With this kind of tempo in creation and production, it’s easy to understand why DCI’s engineering headcount as grown 2x the last 3 years. It’s new people and ideas partnered with engineering veterans, like 30-year team member Rudy Zeller, that keep DCI at the forefront of innovation and delivering quality, helpful tools for customers in the HDD industry. Designing and developing equipment that is going underground in varying extreme conditions is no easy task. Pendergrass continues:
“We create receivers and transmitters that use a quasi-static magnetic field to communicate between a below-ground transmitter and an above-ground receiver. It’s a severe signal-to-noise ratio problem, and a system design issue. Our engineers must optimize an entire system to assure good communication in the presence of many types of soil, all kinds of passive interference like pipes and steel rebar and a growing field of active interference like cell towers and power lines. Additionally, our customers are expecting more and more… more depth, more communication, more data recording, more flexibility in their products, more automation, more and more software-enabled features. These are very challenging technical problems, and we search for the best people to solve them.”
With this level of pressure and performance demands from customers where time spent not drilling equates to loss of profit, delivering highly durable, functional tools that help them work safer and faster is key.
That’s where DCI’s advancements in software come into play. Not only is DCI constantly trying to better our products’ interfaces and UX but also our apps and cloud products, allowing customers to participate in a fully connected suite of tools that help them manage equipment inventory and communication with employees and customers for unparalleled efficiency.
To build and develop software and hardware that work together so well, an open, collaborative environment is necessary. Pendergrass says of the DCI engineering operation:
“Although we have organized our teams to focus on a particular product, we are really creating an entire ‘ecosystem’ of products that must talk to each other. This requires continuous alignment between teams. We have great engineering project managers that are dedicated to working with each other, and it’s in our culture for the engineers to work in a highly collaborative way.”
To maintain freshness of work and collaboration, refinements to the teams’ processes and workloads are regularly reviewed and executed, optimizing for efficiency and ideation. Helping along the way is DCI’s open floor plan as well as the proximity of elements already mentioned: a highly trained and efficient manufacturing team and the ability to test onsite.
As the HDD industry moves into the future and more of the infrastructure that powers the world goes underground, the people and tools that help make that happen will grow in importance. Here at DCI, we’re excited for the challenge and about our engineers, now and in the future, who will help make it happen.
*Are you an engineer and want to help build the future of the HDD industry too? Check out our jobs board for open positions!